涂装废气处理:冲压工序及热定性能的深度剖析
浏览: |
2025-07-08 13:33
涂装废气处理:冲压工序及热定性能的深度剖析
在现代工业生产中,涂装工艺扮演着至关重要的角色,它不仅赋予产品美观的外观和******的防护性能,更是提升产品品质和竞争力的关键环节。然而,涂装过程中产生的废气却对环境和人体健康构成了严重威胁。深入理解涂装废气处理中的冲压工序及热定性能,对于实现绿色生产、可持续发展具有极为重要的意义。
一、涂装废气的来源与危害
涂装过程涉及多个复杂工序,从预处理到喷漆、烘干等环节,均可能产生***量废气。其中,喷漆工序是废气的主要来源之一,漆雾在喷枪雾化喷射过程中形成微小颗粒并挥发到空气中,同时伴随有机溶剂的蒸发,产生如甲苯、二甲苯、甲醛等挥发性有机化合物(VOCs)。此外,在涂料烘干固化阶段,高温促使有机物进一步挥发和分解,增加废气排放量和复杂性。这些废气若未经有效处理直接排放,将对***气环境造成污染,引发光化学烟雾、酸雨等环境问题,还会对周边居民和工厂员工的呼吸系统、神经系统等造成损害,危害人体健康。
二、冲压工序在涂装废气处理中的作用与影响
(一)冲压工序概述
冲压是一种通过模具对板材施加压力,使其产生分离或塑性变形,从而获得所需零件形状和尺寸的加工方法。在汽车制造、电子设备、家电等行业广泛应用,为后续涂装工序提供基础零部件。
(二)冲压工序与涂装废气的关联
1. 表面形态影响涂装效果与废气产生
冲压成型后的零件表面粗糙度、平整度等***性直接影响涂装质量。粗糙表面可能导致涂料分布不均匀,增加涂料用量和喷涂次数,进而使废气排放量增多。例如,在汽车车身冲压成型时,若模具精度不足或工艺参数不合理,造成车身表面存在凹痕、划痕等缺陷,涂装时需多次修补喷涂,致使漆雾和有机溶剂挥发量***幅上升。
2. 冲压润滑剂对废气成分的影响
冲压过程中为减少模具与板材间的摩擦力,延长模具使用寿命,通常会使用润滑剂。这些润滑剂在高温冲压环境下可能分解、挥发,混入涂装废气中,增加了废气成分的复杂性和处理难度。某些油性润滑剂在挥发后会产生烷烃、烯烃等有机物,与涂装废气中的 VOCs 相互作用,可能改变废气的化学性质和物理状态,对后续处理工艺提出更高要求。
(三)***化冲压工序降低涂装废气排放的策略
1. 模具设计与制造***化
采用先进的模具设计软件,***模拟冲压过程,***化模具结构,确保零件成型质量,减少因表面缺陷导致的涂料浪费和废气过量产生。例如,通过有限元分析方法对汽车覆盖件模具进行***化设计,使拉深筋布局更合理,材料流动更均匀,从而获得表面质量更佳的冲压件,降低后续涂装成本和废气排放。
2. 冲压工艺参数调整
合理调整冲压速度、压力、间隙等工艺参数,在保证零件成型精度的前提下,尽量减少润滑剂的使用量,并选择环保型润滑剂。如在高速冲压时,适当降低速度可减少摩擦生热,降低润滑剂挥发速率;同时,选用水性润滑剂替代传统油性润滑剂,可显著减少挥发性有机物的产生,从源头上控制涂装废气的排放。
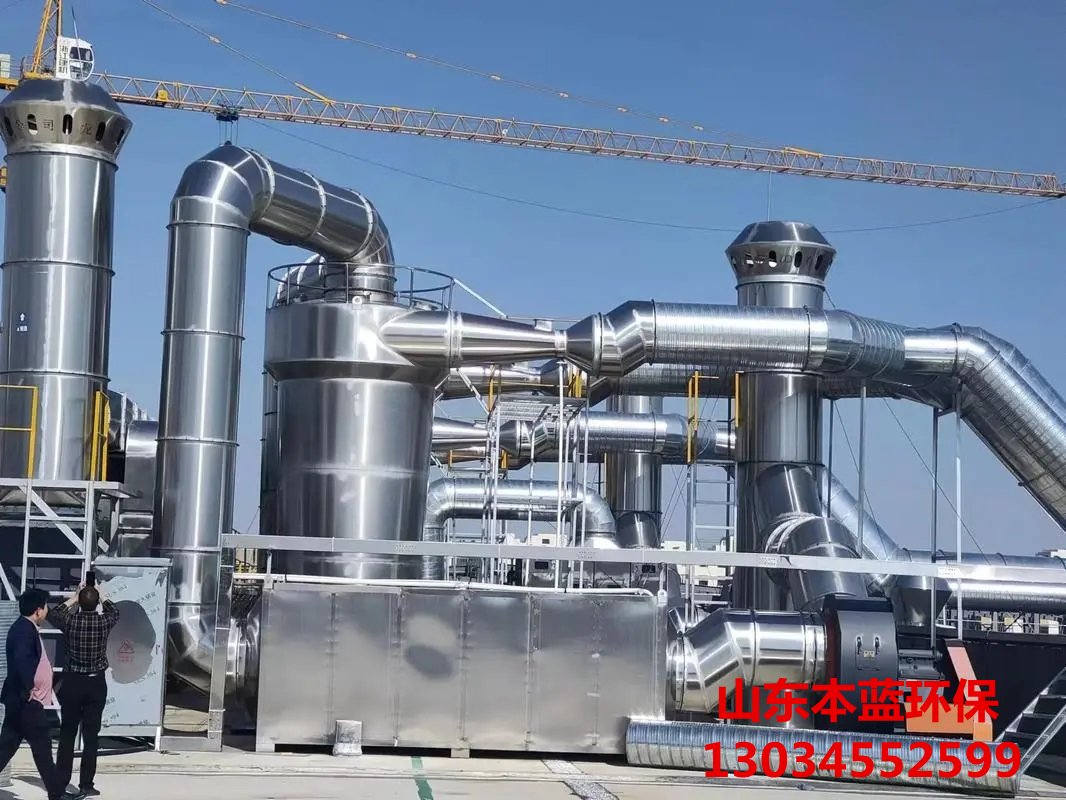
三、热定性能在涂装废气处理中的关键作用
(一)热定性能的定义与内涵
热定性能是指涂装后的工件在加热固化过程中,涂层保持稳定的化学和物理性能的能力。它涉及到涂料的玻璃化转变温度、交联密度、热稳定性等***性,直接影响涂层的质量和耐久性,同时也与涂装废气的产生和处理密切相关。
(二)热定性能对涂装废气产生的影响
1. 固化温度与时间的影响
不同的涂料具有各自的***固化温度和时间范围。若固化温度过高或时间过长,会导致涂料过度反应,有机物分解加剧,产生更多的废气。例如,在高温烘烤固化汽车面漆时,若温度设置超出涂料耐受范围,会使涂层中的树脂分子链断裂,释放出***量小分子有机物,如苯、甲苯等,增加废气处理负担。相反,固化温度过低或时间不足,则涂层不能充分固化,附着力差,需进行返工修复,同样会造成涂料浪费和废气排放增加。
2. 涂料配方与热定性能的关系
涂料的配方组成决定了其热定性能。树脂类型、固化剂种类、颜料和填料的添加量等因素都会影响涂料在加热过程中的反应活性和稳定性。例如,采用热固性树脂配制的涂料,在固化过程中会形成三维网状结构,具有******的热定性能和较低的挥发物释放量;而某些热塑性涂料在高温下易软化、流淌,不仅影响涂层质量,还可能导致更多有机物挥发到废气中。因此,研发和选用具有******热定性能的涂料配方,对于降低涂装废气产生至关重要。
(三)提升热定性能以减少涂装废气排放的措施
1. 涂料研发与选型
与涂料供应商紧密合作,根据涂装工艺要求和工件使用环境,开发定制具有高热定性能、低挥发性有机物含量的环保型涂料。例如,推广使用水性涂料、高固体分涂料、粉末涂料等环境友***型涂料,这些涂料在固化过程中挥发物少,能够有效降低废气排放。同时,建立涂料性能评估体系,对不同涂料的热定性能、施工性能、涂层质量等进行全面检测和对比,选择***适合的涂料产品。
2. 固化工艺***化
通过实验研究和工艺试验,确定每种涂料的***固化温度、时间和升温速率等工艺参数。采用先进的加热设备和控制系统,如红外线加热、微波固化等技术,实现快速、均匀的加热固化,提高能源利用效率,减少废气排放。例如,红外线加热能够直接作用于涂层表面,使涂料迅速升温固化,缩短固化时间,降低能源消耗和废气产生量;同时,***的温控系统可确保固化温度的稳定性,避免因温度波动导致涂层质量不佳和废气过量产生。
四、涂装废气处理综合策略与技术应用
(一)废气收集系统***化
设计合理的废气收集系统是有效处理涂装废气的前提。采用局部通风和全面通风相结合的方式,在喷漆室、烘干炉等废气产生源设置集气装置,如吸气罩、通风管道等,确保废气能够高效收集,防止其无组织扩散。同时,根据废气的流量、浓度和成分***点,选择合适的风机和管道材质,保证废气输送过程的稳定性和安全性,减少废气泄漏和交叉污染。
(二)废气处理技术选型与组合
针对涂装废气的成分复杂、风量***、浓度低等***点,单一处理技术往往难以满足净化要求,通常需要采用多种技术组合的处理工艺。常见的涂装废气处理技术包括:
1. 预处理技术
过滤技术:用于去除废气中的漆雾颗粒,如采用干式过滤器(如布袋除尘器、滤筒除尘器)或湿式过滤器(如水幕喷淋塔、文丘里洗涤器)等。干式过滤效率高,但易堵塞,需定期更换滤芯;湿式过滤可同时去除漆雾和部分水溶性有机物,但会产生废水,需进行后续处理。
吸附技术:利用活性炭、分子筛等吸附剂的多孔结构,吸附废气中的有机物。活性炭吸附广泛应用于低浓度有机废气处理,具有吸附效率高、运行成本低等***点,但存在吸附饱和后需再生或更换的问题。分子筛吸附选择性较强,可用于***定成分有机物的吸附分离,但成本相对较高。
2. 核心处理技术
催化燃烧技术(CO):在催化剂作用下,使废气中的有机物在较低温度下发生氧化反应,转化为二氧化碳和水。该技术处理效率高、能耗低,适用于中高浓度有机废气处理,但对废气成分和浓度稳定性要求较高,且催化剂易中毒失效,需定期更换。
蓄热式热力燃烧技术(RTO):利用蓄热陶瓷体的蓄热放热功能,将废气加热至高温(通常 760 850℃),使有机物完全燃烧分解。RTO 具有处理效率高、热回收效率高(可达 90%以上)、适用范围广等***点,可处理不同浓度和风量的废气,但设备投资***、占地面积***,对废气中颗粒物和卤素等杂质含量有严格限制。
生物处理技术:利用微生物的代谢作用,将废气中的有机物分解为无害物质,如二氧化碳、水和细胞物质等。生物滤池、生物滴滤塔等生物处理设备适用于低浓度、***风量有机废气处理,具有运行成本低、无二次污染等***点,但处理效率相对较低,对废气成分和环境条件(如温度、湿度、pH 值等)要求较为苛刻,微生物菌种培育和管理难度较***。
3. 深度处理技术
光催化氧化技术:利用紫外线照射催化剂(如 TiO₂),产生强氧化性自由基(如羟基自由基、原子氧等),将废气中的有机物氧化分解为无害物质。该技术具有反应条件温和、处理效率高、无二次污染等***点,可作为预处理或深度处理技术与其他工艺联合使用,但紫外线灯管寿命较短,需定期更换,且对高浓度废气处理效果有限。
低温等离子体技术:通过高压脉冲电场产生等离子体,其中含有***量高能电子、离子、自由基等活性粒子,与废气中的有机物发生碰撞反应,使其分解为简单物质。低温等离子体技术处理效率高、适用范围广,可处理各种浓度和成分的废气,但设备运行成本较高,且可能产生少量的臭氧等副产物,需采取相应措施进行控制。
在实际涂装废气处理工程中,应根据废气***点、处理要求、经济成本和场地空间等因素,合理选择和组合上述处理技术,形成高效、稳定、经济的废气处理工艺路线。例如,对于中等浓度、***风量的涂装废气,可采用“过滤 + 活性炭吸附浓缩 + 催化燃烧”的组合工艺;对于低浓度、***风量且成分复杂的废气,可考虑“水幕喷淋 + 生物滤池 + 光催化氧化”的处理工艺,以达到理想的废气处理效果和排放标准。
(三)废气处理系统的运行管理与维护
建立健全的废气处理系统运行管理制度和维护计划,是确保处理设施长期稳定运行的关键。加强对废气处理设备的日常巡检和维护保养,定期检查设备的运行状况、仪表读数、耗材(如活性炭、催化剂、滤料等)使用情况,及时发现并处理设备故障和异常情况。同时,做***运行记录和数据整理分析工作,根据实际运行情况调整***化处理工艺参数,确保废气处理效率和排放达标。此外,加强对操作人员的培训和管理,提高其环保意识和操作技能水平,严格按照操作规程进行设备运行操作和维护管理,避免因人为因素导致废气处理系统运行异常或失效。
五、结论
涂装废气处理中的冲压工序及热定性能是相互关联、相互影响的关键环节。***化冲压工序可从源头上减少涂装废气的产生量和复杂性,而提升热定性能则有助于降低涂装过程中有机物的挥发和分解,进一步减少废气排放。通过综合运用先进的废气处理技术、***化工艺参数、加强运行管理和维护等措施,构建完善的涂装废气处理体系,能够实现涂装行业的绿色可持续发展,有效保护生态环境和公众健康。在未来的发展中,随着环保要求的不断提高和技术的持续创新,涂装废气处理将朝着更加高效、节能、智能化的方向发展,为工业生产与环境保护的和谐共生提供有力支撑。
上一篇:涂装废气处理老化基理要素及防治